Service
Chengzhiduo(VFDDRIVE) provides a full range of services covering the entire life cycle of the product, providing guidance and suggestions to customers from initial consultation, product selection to after-sales maintenance to ensure efficient operation of the equipment and timely resolution of customer problems.
Chengzhiduo(VFDDRIVE) can not only provide you with a variety of industrial control products in the automation industry, but also provide you with industry solutions, allowing you to achieve one-stop procurement and one-stop service. Through products and various services, we help you improve equipment performance, reduce maintenance costs, extend service life and reduce comprehensive costs, thereby creating higher profits for customers in the foreseeable future and maintaining a leading position in the highly competitive market.
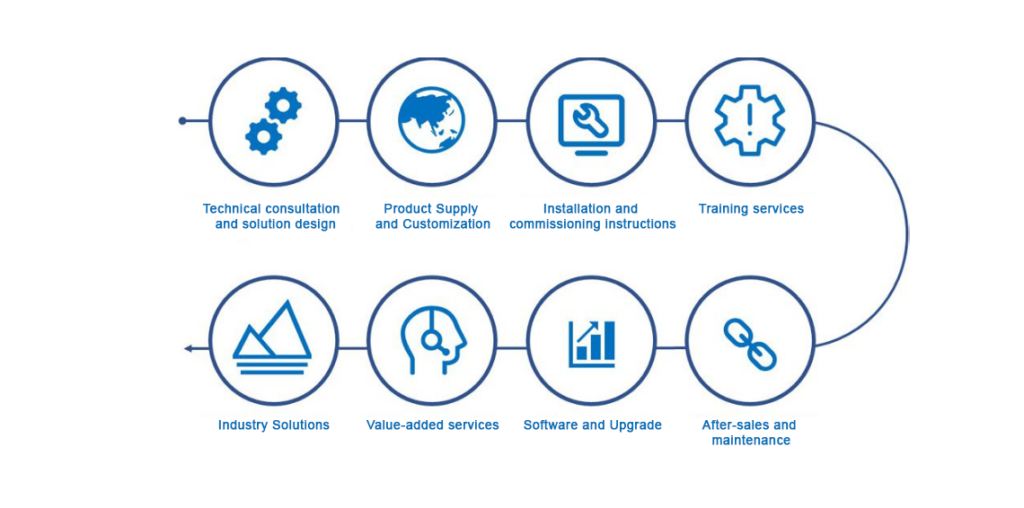
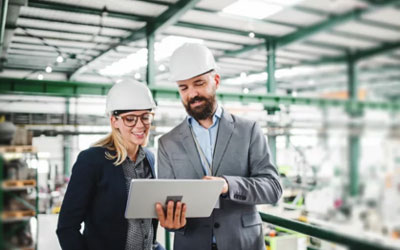
1. Technical consultation and solution design
Demand analysis: Recommend suitable inverter models and power ranges based on customer equipment load types (such as motors, pumps, fans, etc.), process requirements and environmental conditions.
Solution design: Assist in completing electrical system design, including inverter selection, parameter configuration, energy-saving evaluation, etc.
System integration support: Provide electrical drawing design, control logic configuration suggestions, and assist in matching PLC, sensors and other peripherals.
Energy-saving solution: Design energy-saving transformation solutions through energy efficiency evaluation (such as load curve analysis) to reduce customer operating costs.
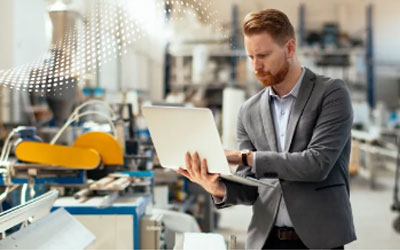
2. Product supply and customization
Standard product supply: Provide general-purpose and industry-specific (such as lifting, textile, HVAC) inverters.
Customized development: Adjust hardware (such as protection level IP65) or software (such as industry-specific algorithms) according to special needs.
Accessories: Supply supporting components such as brake resistors, reactors, filters, etc.
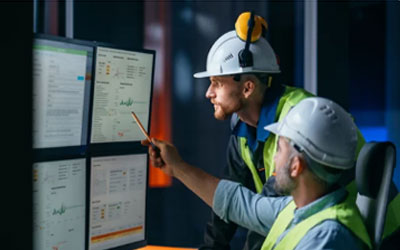
3. Installation and commissioning instructions
Product demonstration: Provide prototype test or simulation demonstration to verify the performance of the inverter.
Installation guidance: Provide installation manual, wiring diagram or remote guidance to ensure correct installation.
Debugging support: Technical engineers provide remote telephone guidance on debugging wiring, parameter setting (such as motor matching, V/F curve, PID control) and communication protocol configuration (such as Modbus, Profibus).
Trial run test: Assist in no-load/load testing, optimize parameters such as starting torque, acceleration and deceleration time, and ensure smooth operation of the equipment.
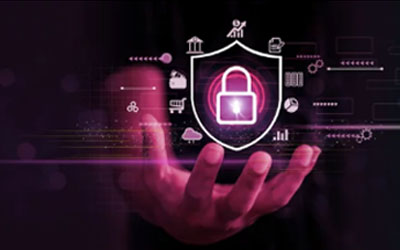
4. Training services
Operation training: training customer operators to master basic operations, parameter settings, fault identification and other basic functions.
Maintenance training: training daily maintenance (such as heat dissipation cleaning), fault diagnosis (such as overcurrent, overvoltage code interpretation) and other skills.
Advanced technical training: advanced content such as PLC linkage programming and network control for engineers.
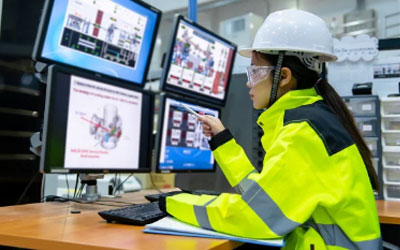
5. After-sales and maintenance
Fault response: Quickly solve unexpected problems through telephone, remote diagnosis or 48-hour on-site service.
Spare parts supply: Provide original spare parts to shorten the maintenance cycle.
Regular inspection: Preventive maintenance, check potential problems such as capacitor aging and fan status.
Warranty service: Free repair or replacement during the warranty period according to the contract, usually 1-2 years warranty, and extended warranty for some key components (such as IGBT).
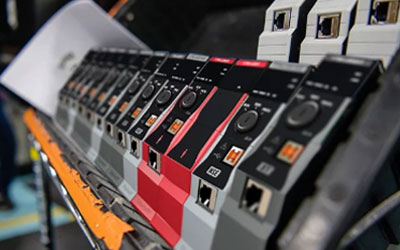
6. Software and Upgrade
Parameter backup: Assist in backing up device parameters to prevent data loss.
Firmware upgrade: Push new functions or compatibility updates (such as support for new communication protocols).
Remote monitoring: Realize device status monitoring and energy efficiency management through the cloud platform.
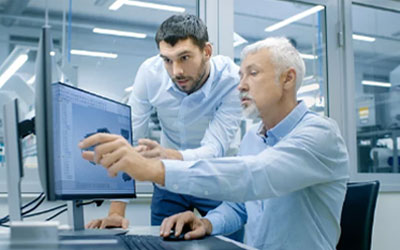
7. Value-added services
Energy efficiency optimization: Analyze operating data and make suggestions for energy-saving transformation.
Customized development: Adjust software and hardware according to special needs (such as communication protocols and industry standards).
Spare parts inventory service: Reserve common spare parts for customers to shorten downtime.
24/7 support: Provide round-the-clock emergency response for key industry customers.
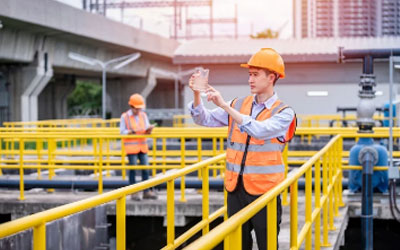
8. Industry Solutions
Provide targeted services for specific industries (such as HVAC, textiles, and lifting).
Manufacturing: Optimize response speed for high dynamic loads such as injection molding machines and conveyor belts, and solve multi-motor synchronization or high-precision speed regulation problems.
HVAC: Optimize the variable frequency control strategy of fans/water pumps to reduce energy consumption.
Water industry: Constant pressure water supply solution to solve the water hammer effect problem.
New energy: Grid adaptation solution for photovoltaic/wind power inverters.